Specialist Suggestions on What is Porosity in Welding and Exactly How to Resolve It
Wiki Article
Comprehending Porosity in Welding: Exploring Reasons, Impacts, and Avoidance Strategies
Porosity in welding is a persistent difficulty that can significantly impact the high quality and honesty of welds. As specialists in the welding industry are well conscious, understanding the causes, effects, and prevention methods related to porosity is critical for achieving robust and reputable welds. By delving right into the origin of porosity, examining its detrimental impacts on weld quality, and exploring efficient prevention methods, welders can enhance their understanding and abilities to generate premium welds constantly. The intricate interaction of factors contributing to porosity calls for a detailed understanding and an aggressive method to make certain effective welding outcomes.Common Root Causes Of Porosity
Porosity in welding is primarily created by a mix of aspects such as contamination, inappropriate securing, and poor gas coverage during the welding procedure. Contamination, in the form of dust, oil, or corrosion on the welding surface, develops gas pockets when heated, resulting in porosity in the weld. Incorrect shielding happens when the shielding gas, typically used in processes like MIG and TIG welding, is unable to completely shield the molten weld swimming pool from reacting with the surrounding air, resulting in gas entrapment and succeeding porosity. In addition, inadequate gas coverage, typically due to wrong circulation rates or nozzle positioning, can leave components of the weld unprotected, enabling porosity to form. These elements collectively contribute to the development of voids within the weld, compromising its integrity and potentially creating architectural concerns. Comprehending and addressing these common reasons are vital actions in preventing porosity and making sure the top quality and stamina of welded joints.Impacts on Weld Top Quality
The existence of porosity in a weld can dramatically compromise the general quality and integrity of the bonded joint. Porosity within a weld produces spaces or dental caries that damage the structure, making it more vulnerable to breaking, deterioration, and mechanical failing. These spaces serve as stress concentrators, reducing the load-bearing ability of the weld and raising the chance of early failure under applied stress and anxiety. In addition, porosity can additionally work as possible sites for hydrogen entrapment, more exacerbating the deterioration of the weld's mechanical residential properties.Moreover, porosity can hinder the performance of non-destructive testing (NDT) techniques, making it testing to discover other issues or stoppages within the weld. This can cause substantial safety worries, especially in important applications where the architectural honesty of the bonded elements is extremely important.
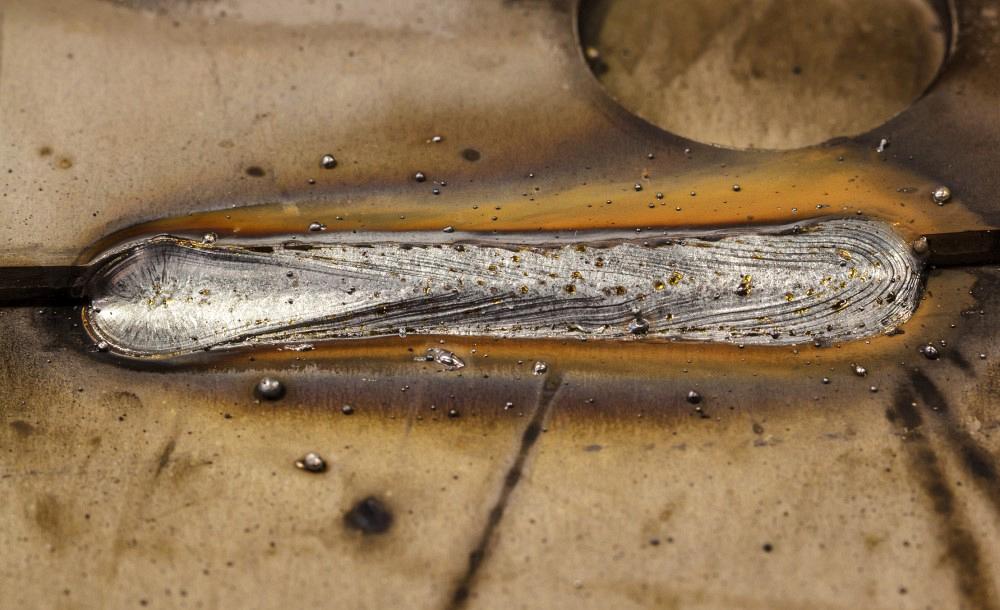
Prevention Techniques Review
Provided the harmful impact of porosity on weld top quality, reliable avoidance strategies are critical to maintaining the architectural honesty of bonded joints. In addition, picking the appropriate welding specifications, such as voltage, existing, and travel rate, can aid lessen the risk of porosity formation. By integrating these avoidance strategies right into welding techniques, the occurrence of porosity can be considerably lowered, leading to stronger and more dependable bonded joints.Importance of Correct Shielding
Appropriate protecting in welding plays a vital function in protecting against climatic contamination and guaranteeing the honesty of bonded joints. Protecting gases, such as argon, helium, or a mixture of both, are typically utilized to secure the weld pool from responding with aspects in the his explanation air like oxygen and nitrogen. When these responsive elements enter into contact with the hot weld swimming pool, they can cause porosity, leading to weak welds with reduced mechanical buildings.Insufficient securing can result in numerous problems like porosity, spatter, and oxidation, endangering the structural honesty of the bonded joint. As a result, sticking to proper protecting techniques is necessary to produce top notch welds with very little issues and guarantee the long life and reliability of the welded elements (What is Porosity).
Monitoring and Control Techniques
Just how can welders properly keep track of and control the welding process to guarantee ideal results and stop flaws like porosity? One trick technique is via the usage of advanced monitoring technologies. These can include real-time surveillance systems that supply responses on criteria such as voltage, existing, take a trip speed, and gas circulation prices. By continually monitoring these variables, welders can identify deviations from the optimal conditions and make immediate adjustments to avoid porosity formation.
In addition, carrying out appropriate training programs for welders is important for monitoring and managing the welding procedure effectively. What is Porosity. Enlightening welders on the significance of preserving constant specifications, such as appropriate gas shielding and travel rate, can assist protect against porosity concerns. Regular analyses and accreditations can also make certain that welders excel in surveillance and managing welding processes
Furthermore, making use of automated welding systems can enhance surveillance and control abilities. These systems can precisely control welding criteria, minimizing the likelihood of human mistake and making certain constant weld quality. By incorporating sophisticated surveillance innovations, training programs, and automated systems, welders can hop over to here properly keep track my latest blog post of and regulate the welding procedure to decrease porosity issues and achieve high-grade welds.
Final Thought

Report this wiki page